Tilting Bench for Composite Hood Bonding – Bonding Jig Project
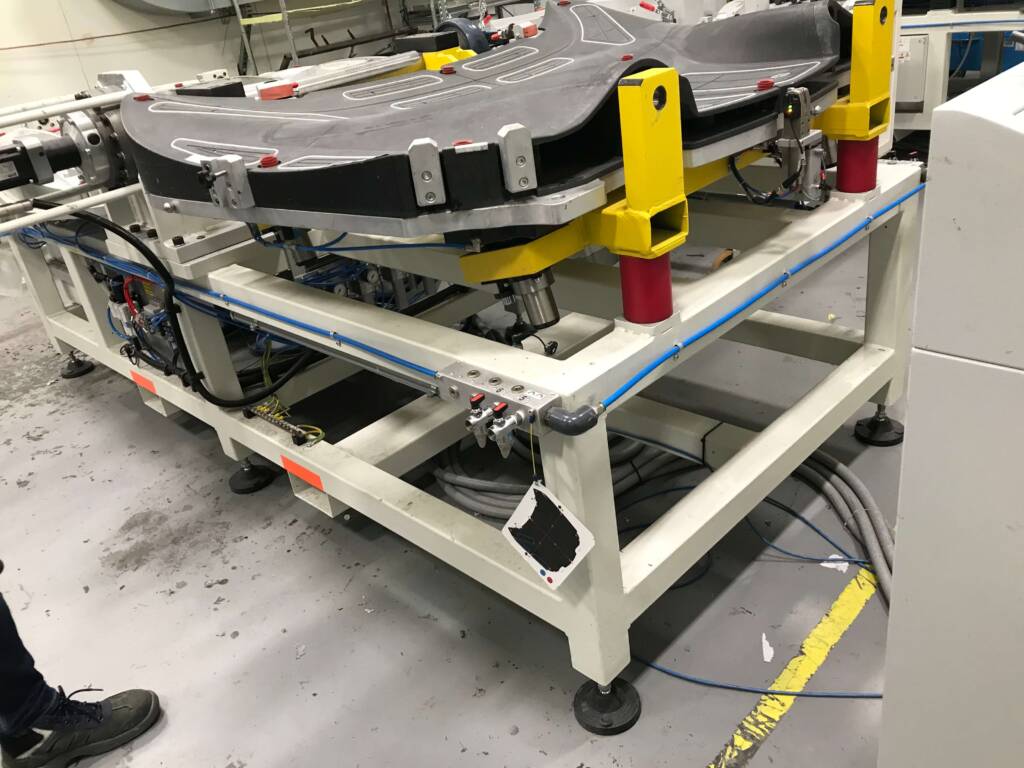
Issue Identified:
A company operating in the composite materials sector needed to improve the bonding process for semi-shells of composite hoods.
The existing manual process was affected by:
Alignment difficulties during bonding
Inadequate temperature control during curing
Operator safety concerns during handling phases
The main objective was to develop an automated bench that would ensure:
Correct positioning of the shells during bonding
Accurate temperature control in critical bonding areas
Safe and precise tilting of the assembly during the process
Solution:
A tilting bench named “Bonding Jig” was designed and built, featuring:
Powder-coated steel frame
Dual-sided jigs (aluminum inner, resin outer), with high-precision machining and integrated electric resistances for thermal control
Mixed motorization system (epicyclic/worm gear) for controlled and safe tilting, with adjustable speed from 0.1 to 3.5 rpm
Cartridge electric heating system (7.2 kW total), managed via dedicated thermocouples
Cycle management via Siemens PLC (Simatic S7-1200) and HMI on panel PC with custom LabVIEW software
Integrated Features:
Pneumatic clamping systems
Vacuum sensors to detect correct part placement
Remote supervision via dedicated hardware/software module for online support and diagnostics
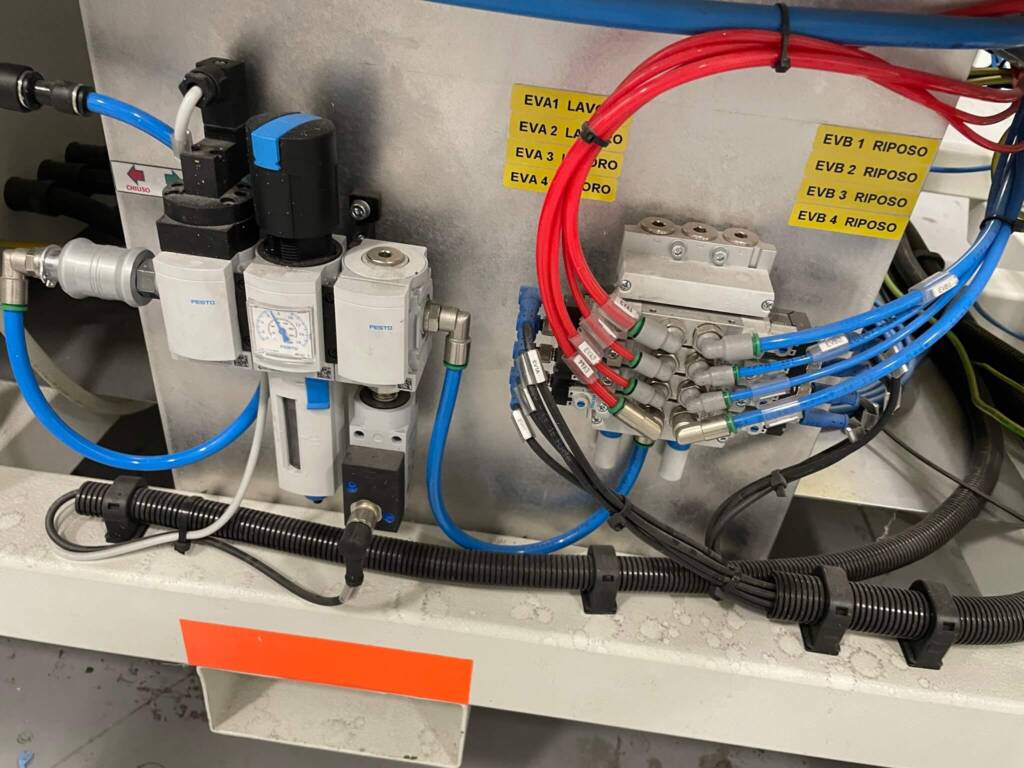
Results Achieved:
Increased process efficiency: reduced positioning and bonding time
Precise curing temperature control, essential for final product quality
Improved operational safety through automated tilting management
Reliability and repeatability via semi-automated digital control
Remote support: diagnostics and software updates without on-site intervention
Contact us for a Custom Quote
Tailored solutions for your industry’s specific needs. Our experts are ready to support you.
Customized solutions for every industrial sector
Dedicated consulting at every project stage
Specialized and continuous technical support
Technological innovation to enhance operational efficiency