Continuous Monitoring System for a Glass Factory – ATEX Project
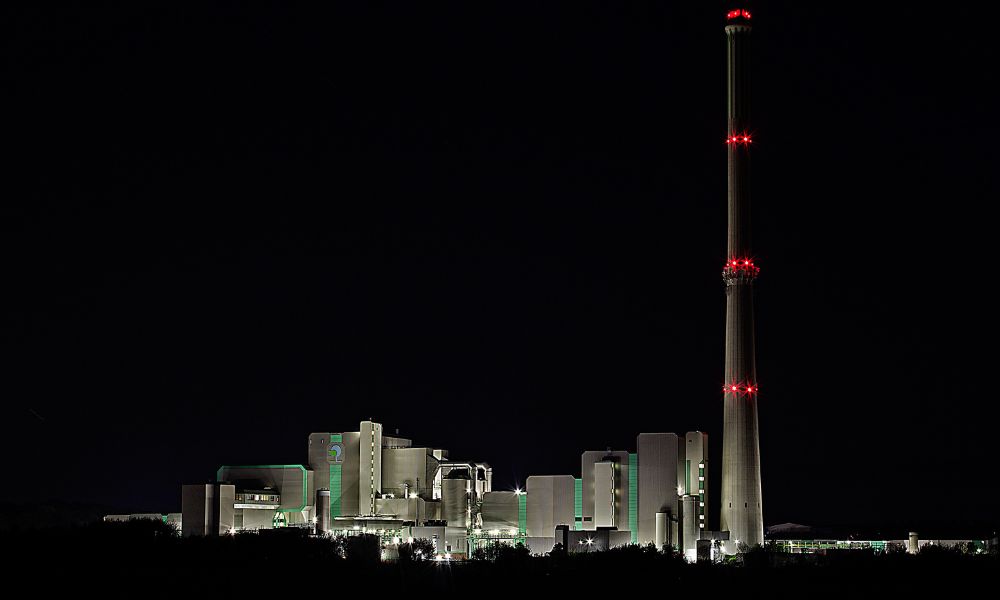
Identified Challenge
The public waste-to-energy plant for municipal and medical waste was equipped with an FTIR analysis system that frequently malfunctioned, causing repeated plant shutdowns with critical impacts on the continuity of the waste disposal service.
The system was required to monitor the following parameters on each measurement line:
CO, CO₂, SO₂, NO, NO₂, O₂, NH₃, HCl, TOC, Hg, dioxins (sampling), dust, flow rate, and temperature.
After analyzing the situation, the client turned to Opus Automazione to identify the root causes of the malfunctions and provide an effective solution.
Solution:
The technical analysis revealed that the flue gas treatment system, equipped with a scrubber, increased the water vapor (H₂O) concentration to around 60%, causing condensation to form in the FTIR measurement chamber, which operated at 180 °C. This condensation damaged the optical mirrors, preventing accurate data acquisition.
The intervention carried out by Opus Automazione included:
Design and modification of the gas sampling and treatment system to maintain the temperature above 160 °C, reducing the risk of condensation.
Revision of the measurement chamber heating system, which was not provided by the instrument’s original manufacturer, with corresponding technical documentation.
Development of a cost-benefit analysis to support the final decision-making process.
Replacement of the FTIR analyzer with an 8-channel multiparameter system, more reliable and suitable for the plant’s specific operating conditions.
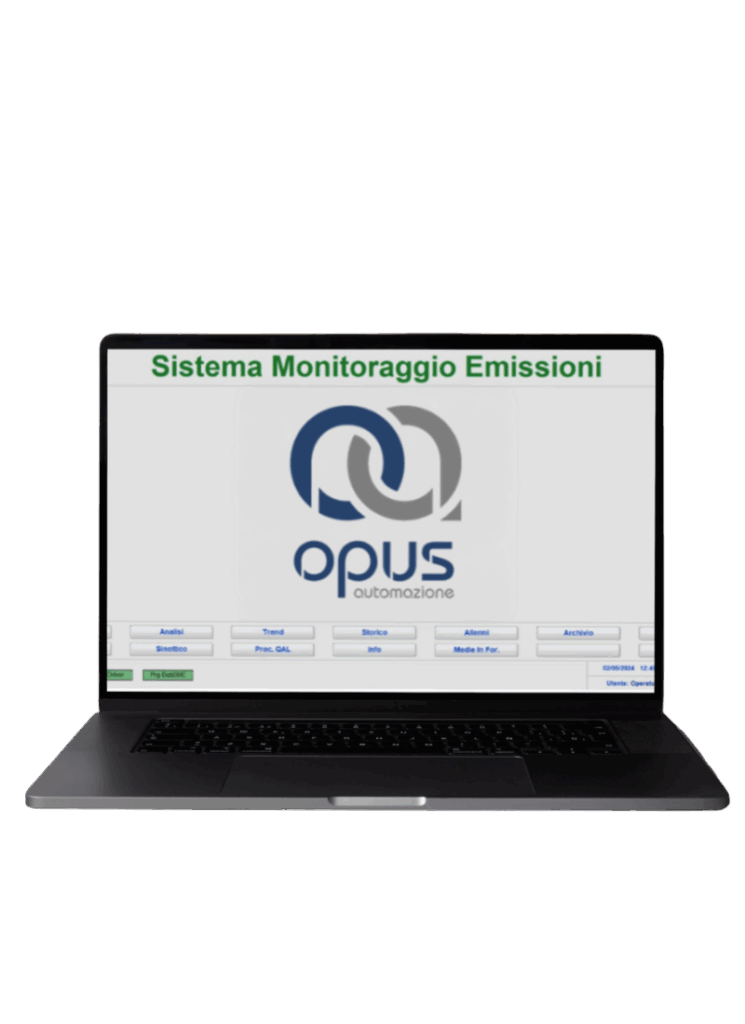
Results Achieved
Operational stability and data reliability:
The replacement of the FTIR system with a multiparameter analyzer solved condensation issues, ensuring operational continuity and analytical accuracy.- Plant scalability: Following the intervention, the facility was able to expand over time, adding a second incineration line. Currently, three gas lines operate with automatic switching across two multichannel analyzers.
- Data redundancy and security: The new data acquisition system complies with current regulations and includes hot redundancy of servers, ensuring maximum data availability and environmental data security.
Explore more case history
Contact Us for a Customized Quote
Tailored solutions for the specific needs of your industry. Our experts are ready to support you.
Custom solutions for every industrial sector.
Dedicated consulting for every phase of the project.
Specialized and continuous technical support.
Technological innovation to improve operational efficiency.