Continuous Emissions Monitoring System for a Glass Plant – ATEX Project
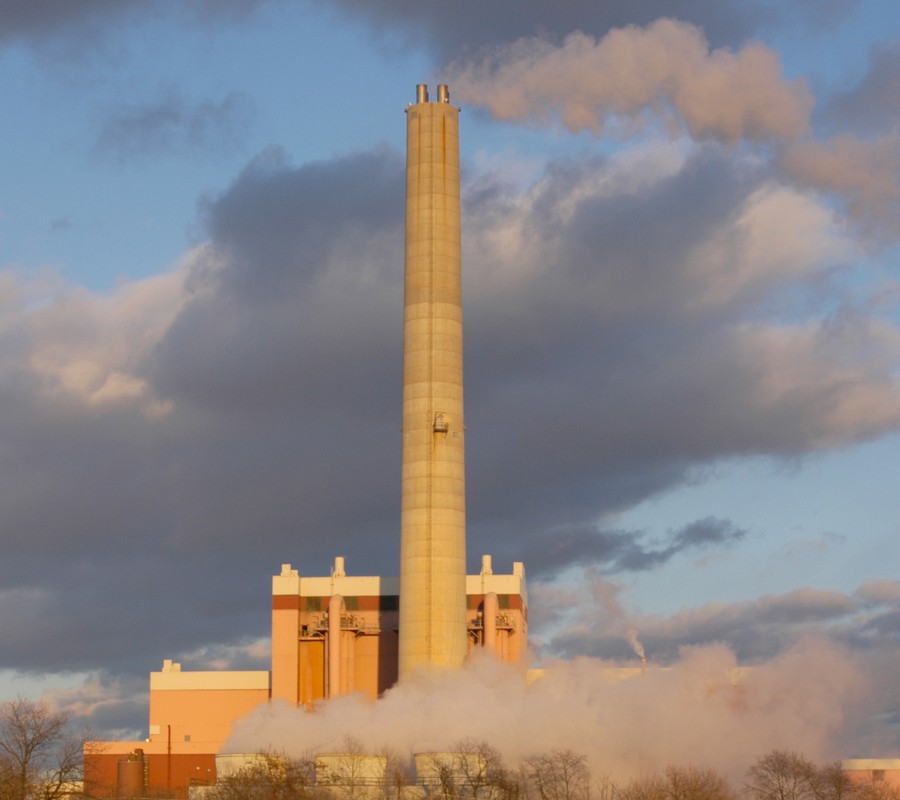
Identified Challenge
The client, an industrial glass manufacturer, needed to carry out a major revamping of its electric furnace, including the installation of a new chimney and a modern Continuous Emissions Monitoring System (CEMS).
The new CEMS had to measure the main pollutants and physical parameters: SO₂, NO, NO₂, O₂, dust, flow rate, and temperature. The entire system had to be supervised by a SCADA compliant with European and Italian regulations.
A key challenge identified during the project concerned the ATEX classification of the area adjacent to the chimney, which was classified as a hazardous zone according to the Ex directive.
Solution:
Opus Automazione designed and implemented a sampling and analysis system fully compliant with Ex II2G T6 standards, addressing all the complexities of the installation environment.
The main technical actions carried out included:
Design and construction of a continuous sampling system suitable for ATEX-classified areas.
Selection and installation of Ex-proof instruments on the chimney.
Placement of analyzers inside a shelter with pressurized electrical panels, ensuring operational safety.
Custom gas treatment to neutralize the SO₃ component, which is highly corrosive to instrument cells and optical components.
Installation of DatiSME software, compliant with current regulations, on three different workstations: local, environmental manager, and plant management.
Project completion with commissioning, final testing, and operator training.
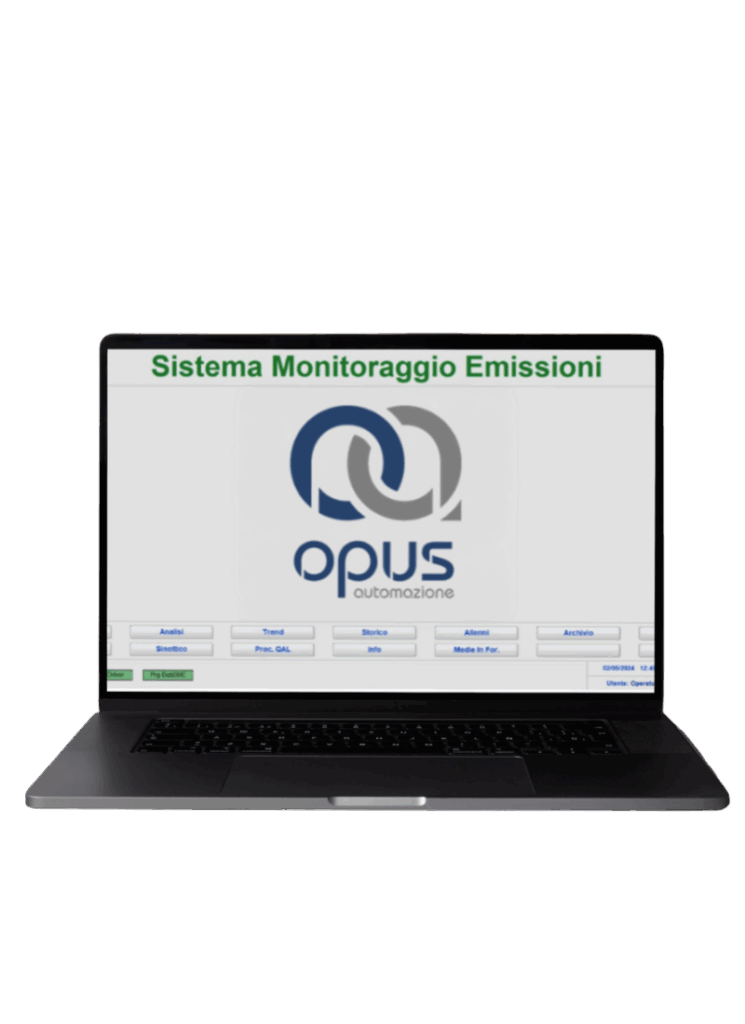
Results Achieved:
ATEX compliance ensured:
The entire CEMS was designed to operate in hazardous areas, fully complying with Ex II2G T6 standards, ensuring installation safety.Protection of analyzers from SO₃:
The preventive maintenance service minimizes the risk of failures or malfunctions, ensuring stable and environmentally compliant energy production.Immediate operability and personnel training:
On-site training and final testing enabled a smooth commissioning process, reducing system startup times.Centralized supervision and traceability:
The dedicated SCADA system provides real-time supervision and complete traceability of all key parameters.
Explore More Case History
Contact Us for a Customized Quote
Tailored solutions for the specific needs of your industry. Our experts are ready to support you.
Custom solutions for every industrial sector.
Dedicated consulting for every phase of the project.
Specialized and continuous technical support.
Technological innovation to improve operational efficiency.